API Synthesis in Flow: Benefits of Micro to the Plant
Over the last two decades, continuous flow chemistry has received intense interest and development as applied toward the transformation of organic chemicals. Significant pharmaceutical industry adoption has followed because micro- and meso-scale reactors provide precise control of reaction parameters. This control is of particular interest to the process chemist whose goal is to safely produce syntheses of the highest reliability and limit impurities of an active ingredient.
Many of the advantages of flow stem from the small features of the reaction system, principle of which is a high surface area to volume ratio. The micro-features allow:
- Excellent heat transfer
- Ultrafast mixing
- Large interfacial area and high mass transfer
- High and uniform light efficiency
Heat Transfer
Rapid heat transfer is an enabling attribute which distinguishes flow chemistry from batch. The rate at which heat is added to or removed from a system can influence regio, chemo, and stereoselectivity, reaction yield and the quantity of byproducts formed. It can also enable otherwise prohibitive highly exothermic reactions to be run in a safe and controlled manner and to run reactions at higher temperatures and concentrations.
A visual example illustrating heat transfer efficiency enhancement under flow conditions is shown in Figure 1, considering two containers with different geometry – flask or tubing – containing 1 L of water. Batch analogy would be using a cube (simplified flask) and flow a thin tube. In the case of batch, 1 L of water fits in a 10 cm edge cube which corresponds to 600 cm2 surface area. In flow, using a 0.1 cm edge square tube (simplified tubing), the same amount of water fills 1 km of tubing which corresponds to 40000 cm2. Intuitively, one can see that heat transfer efficiency in the tube is much higher than in the cube due to a greater interaction between the fluid and the container walls (~ 67 times larger).
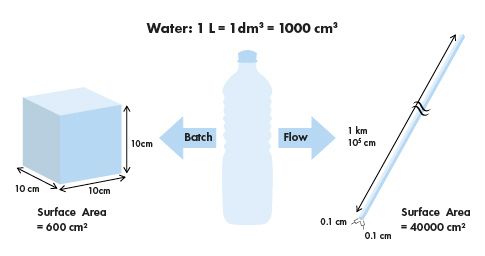
2. Ultrafast Mixing
Accessing flash chemistry (extremely fast reactions) through excellent mixing is another enabling attribute of continuous flow. In mixing sensitive reactions, the benefit is often realized in the form of improved yield and selectivity. Such reactions exhibit reaction rates fast enough to result in significant conversion during the mixing of reagents.
A visual example illustrating the importance of mixing is shown in Figure 2, considering a sensitive reaction between reagents A and B to form product C, where product C can further react with reagent B to form side-product S. When the rate of mixing (transport) is greater than the reaction of A and B, mostly C is formed because B has been fully consumed during the reaction with A (Figure 2 left). On the other hand, when the rate of mixing is less than the rate of reaction, product C will be in contact with unreacted B generating higher amounts of S (Figure 2 right). Incomplete conversion or formation of undesired products leads to yield loss. Further, impurities formed as a result of poor mixing will become a serious cause for concern regarding the API purity profile.
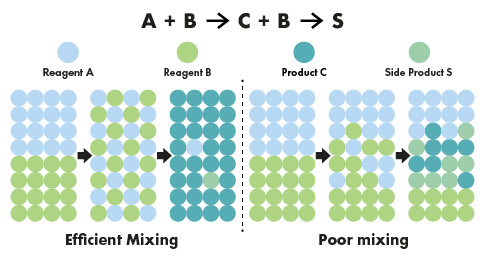
3. Large Interfacial Area and High Mass Transfer: Biphasic Reactions
Accelerating rate of biphasic reactions is a hallmark of continuous flow chemistry. This is a result of the large interfacial areas observed from segmented (slug) flow in microreactors (Figure 3) and the high degree of mixing (Taylor flow) that occurs within each pocket of liquid (Figure 4). Judicious reactor design presents several solutions to the challenges of handling liquid-liquid and gas-liquid biphasic systems. Ensuring constant, vigorous mixing is one means to maintain high interfacial areas. This can be done by incorporating elements that promote mixing throughout the reaction zone.
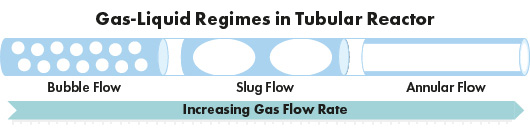
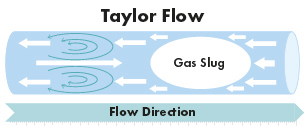
Hydrogenations and aerobic oxidations are ideal candidates for continuous processing. They can be highly exothermic and mass transfer limited, have potential for thermal runaway and involve inherently hazardous reagents (H2, O2). Operating in flow is a convincing strategy to mitigate the associated safety concerns.
4. High and Uniform Light Efficiency: Photochemistry
One of the critical aspects in scaling up photochemistry is the photon transport limitations. As stated by the Lambert-Beer law, light absorbance is proportional to path length and concentration. Increase of reactor (flask) internal diameter decreases the light penetration efficiency (Figure 5: Batch PhotoChem) and thus, longer reaction times are required, generally associated with an increased impurity profile.
A surge of interest in organic photochemical transformations occurred simultaneous to Booker-Milburn’s seminal publication detailing the benefit of UV-transparent fluorinated ethylene propylene (FEP) tubing for continuous flow photoreactors (Figure 5: Flow PhotoChem). The increased surface area in microreactors provides higher light flux, enhancing efficiency and reaction rates thus providing line of sight toward use of photochemistry in a practical manner.
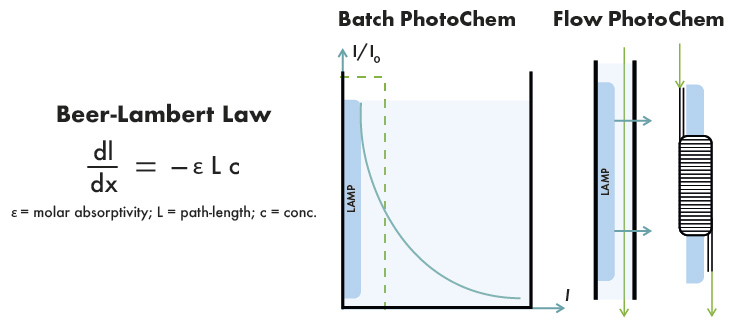
Flow chemistry implementation in API manufacturing presents several advantages to better control process parameters. There is a clear support from regulatory agencies within the pharmaceutical industry for the incorporation of continuous manufacturing processes to ensure a high standard of safety and product quality. Flow chemistry is not a solution to all chemistry problems but if a reaction is sensitive to heat transfer, mixing and mass transfer or involves hazardous reagents and/or unstable intermediates most probably it will benefit from being run in flow.
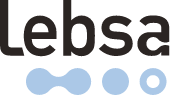
Mateo Berton, PhD
R&D Project Manager
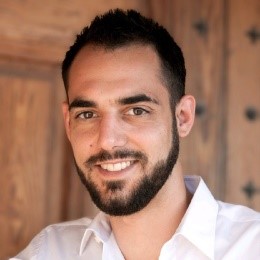
Full article: Berton, M., de Souza, J.M., Abdiaj, I., McQuade, D. T., Snead, D. R. J Flow Chem 2020, 10, 73–92. Scaling continuous API synthesis from milligram to kilogram: extending the enabling benefits of micro to the plant. https://doi.org/10.1007/s41981-019-00060-x