Implementing LEAN Methodology will benefit efficiency, production, time to market and customer satisfaction
Along with SGS, we implemented at LEBSA one of the most exciting projects, starting in 2020. We are talking about the “LEAN project”, which has one primary objective for us: facing the current challenges in the manufacture of Active Pharmaceutical Ingredients (APIs) considering all of its facets to achieve an improvement of process management and organizational efficiency.
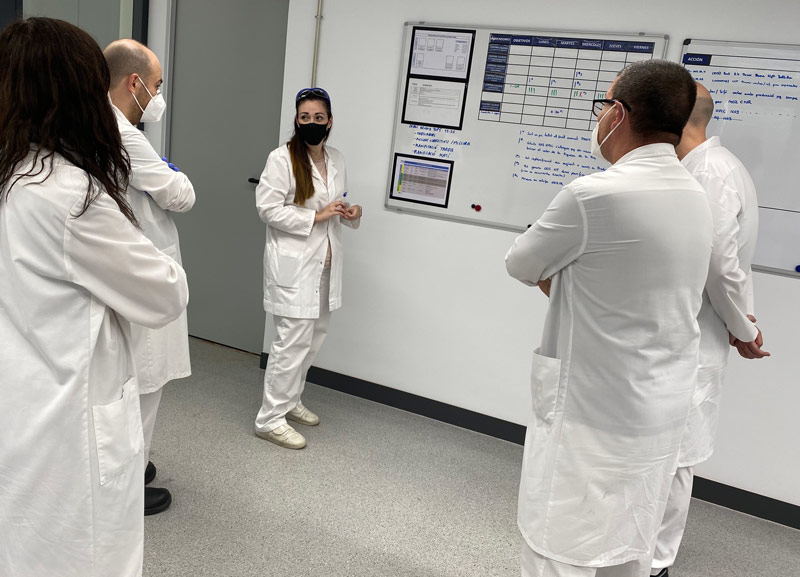
How are we applying LEAN Methodology at LEBSA? What have we achieved so far?
LEAN Methodology and its application at LEBSA
LEAN Methodology is thought to evaluate and improve all of the company’s processes to maximize profits and minimize waste.
With that in mind, we started employing Kaizen methodology in our quality control department. This Methodology comes from the Japanese words “Kai” and “Zen,” which roughly means “change for the better.” The same Methodology is also meant to be implemented in subsequent areas.
As the name implies, this Japanese Methodology is oriented to a continuous improvement of the processes to eliminate any inefficiency encountered on a day-to-day basis. Thus, by adopting the LEAN Methodology, our main goal is to improve the efficiency of the internal processes, maintaining the rigor and high-quality that characterizes our brand.
Our present and future achievements
Implementing LEAN Methodology is quite a challenge in a company with many variables and processes. Still, at LEBSA, we have made considerable progress in this regard. Our organization, operations, facilities, and future projects have been evaluated. Several improvements have been made, and others are yet to come.
So far, we have successfully accomplished several of our goals. What have we achieved to date?
- New laboratory facilities, optimized and carefully planned to implement LEAN Methodology.
- Improvements in the transmission of information with the QC department and other areas of the company.
- Value stream map analysis with individualized attention to every step of the process, aiming to detect weak spots and suggest improvements.
- Detecting indicators and implementing new strategies, defining KPIs that does provide an added value.
If you want to stay up-to-date with our advances and recent developments, stay tuned with our updates and the most recent revisions in our official website. For more information about our services you can contact us here.